最新鋭で最高の製品を生み出す
株式会社 寿原テクノス福岡ファクトリーの超音波スピンドル
株式会社 寿原テクノス福岡ファクトリーの思い
株式会社 寿原テクノス福岡ファクトリーは、一般的な石英ガラス加工方法として「超音波スピンドル」を皆さまに認識いただき、さらなる普及を目指しています。
私たちが手掛ける「超音波スピンドル」は多くの可能性を秘めた技術です。そのために日々、技術の向上・革新を目標に掲げ、石英ガラス加工のプロフェッショナルとして進化し続けています。
超音波加工 具体的な事例
ジルコニア穴加工
超音波スピンドルは穴がテーパーにならない!
超音波スピンドルは内部に超音波振動子が組み込まれているため、ステップ加工で効果を発揮します。
超音波スピンドルのステップ加工とグラインディングセンターのヘリカル加工を比較しました。超音波スピンドルのステップ加工は上下面穴直径の変化が抑えられます。
超音波ステップ加工 | ミーリングヘリカル加工 | |
---|---|---|
加工条件 | ||
ワーク | ジルコニア厚さ10.8mm | ジルコニア厚さ10.8mm |
加工 | 貫通穴加工 | 貫通穴加工 |
ダイヤモンド電着砥石 | φ2.2 #100 | φ1.5 #140 |
主軸回転数(min-1) | 4000 | 8000 |
切込み量(mm) | 0.01 | 0.01 |
送り速度(mm/min) | 2 | 55 |
結果 | ||
加工時間(分) | 22 | 53 |
上面穴直径(mm) | φ2.18 | φ2.15 |
下面穴直径(mm) | φ2.16 | φ2.07 |
直径の差(mm) | 0.02 | 0.08 |
加工結果
下穴が微小テーパーのためネジ切り後のネジ奥が挿入しずらいなどがなく精度が安定します。また加工時間は通常ヘリカル加工の半分以下で加工可能。
リスモツール製ハイブリッド電着工具と相性が良い! その1
窒化ケイ素にハイブリッド電着工具を使用、超音スピンドルの効果で安定した研削の検証。
加工条件 | ||
---|---|---|
ワーク | 窒化ケイ素 | |
加工 1 | ザグリ加工深さ 0.5mm | |
加工 2 | ザグリ加工深さ 3.0mm | |
ツール | リスモツール製ハイブリッド電着ツールφ3 #200 刃長5mm | |
主軸回転数(min-1) | 6000 | |
切込み量(mm) | 0.005 | |
送り速度(mm/min) | 300 | |
結果 | ||
チッピング | 0.1mm以下 非常に良好 |
加工結果 1
加工結果 2
リスモツール製ハイブリッド電着工具と相性が良い! その2
目詰まりしやすく非常に欠けやすい窒化アルミ、超音波スピンドルとリスモーツール製ハイブリッド電着ツールのコンビでチッピングレスの検証。
加工条件 | ||
---|---|---|
ワーク | 窒化アルミ | |
加工 1 | ザグリ加工深さ 1.0mm | |
加工 2 | ザグリ加工深さ 4.0mm | |
ツール | リスモツール製ハイブリッド電着ツールφ3 #400 刃長5mm | |
主軸回転数(min-1) | 8000 | |
切込み量(mm) | 0.01 | |
送り速度(mm/min) | 300 | |
結果 | ||
チッピング | 0.1mm以下 非常に良好 |
加工結果 1
加工結果 2
超音波スピンドルとは?
通常のスピンドル同様ダイヤモンド電着ツールを回転させると同時に、上下に振動させガラス等脆性材料を微破砕しながら加工できるスピンドルです。
超音波スピンドルは内部に超音波振動子が組み込まれています。
超音波振動子に発振器から交流電圧を加えると超音波振動子が伸び縮みし、この振動をダイヤモンド電着ツール先端まで効率よく伝えます。
株式会社 寿原テクノス福岡ファクトリーは40kHzの超音波振動子を採用していますので、ツール先端が1秒間に4万回/振幅1~15μm*1振動します。
*1:振幅量は超音波発振器のボリュームつまみで変更可能。ツール形状によって振幅量は異なります
超音波スピンドルと通常スピンドルの違い
超音波スピンドル(40kHz) | 通常のスピンドル | |
---|---|---|
1 | ダイヤモンド電着ツールを取付ける | ダイヤモンド電着ツールを取付ける |
2 | 主軸回転→ダイヤモンド電着ツールが回転する | 主軸回転→ダイヤモンド電着ツールが回転する |
3 | ダイヤモンド電着ツールを超音波振動させる(上下方向) | |
4 | 回転及び微細振動したダイヤモンド電着ツールで材料を加工 | 回転したダイヤモンド電着ツールで材料を加工 |
超音波スピンドルの仕組み
-
株式会社 寿原テクノス福岡ファクトリーの超音波スピンドルは40kHz
スピンドル内部に組み込まれたアクチュエータ(超音波振動子)に電圧を印加することで40kHz(1秒間に4万回)の超音波振動が発生します。
この超音波振動が
・ツール先端まで効率よく伝えられるように
・ツール先端がZ軸方向にのみ振動するように
アクチュエータ、ブースター、ツールホルダー及びツールは40kHzで共振(共鳴)するよう設計、調整されています。(画像01/超音波共振による伸縮の概要)
-
-
・共振が取れていない場合
⇒アンプに負担、異常発熱⇒スピンドルの破損・ツールの長さが未調整の場合
⇒ツール先端が斜めまたは横方向に振動
⇒品質悪化、ツール寿命の低下株式会社 寿原テクノス福岡ファクトリーの超音波スピンドルは効率よく共振(共鳴)します。
主軸15,000min-1回転、24時間連続稼働時もツール先端がZ軸方向に超音波振動し、抜群の安定感がございます。実際はZ軸方向(p-p)2μm~20μm(アンプ出力で調整)程度の振幅量になります。
超音波共振中はこの超音波振動を4万回/秒行っており、ガラス、サファイア、Si(シリコン)等の脆性材料穴加工に絶大な効果がございます。 -
はやめ
ゆっくり
超音波スピンドルの効果
目詰まりや加工抵抗が驚くほど低減します。
ダイヤモンド電着ツール目詰まり低減 | 加工抵抗低減 |
---|---|
微破砕効果で加工時間 短 洗浄効果でツール寿命 延長 深穴加工 アスペクト比1:15以上 (工具径によっては1:40以上も可能) |
ツール摩耗低減、加工穴径が安定 ダメージレス加工 粗いメッシュのツールでもクラックが浅い |
ダメージレス、クラックが浅い
石英ガラスφ1.5ステップ加工後に同じ時間鏡面磨きを実施
・ステップ加工
・ツール:ダイヤモンド電着ツール#400
・主軸回転数:4000min-1
・送り速度:2mm/min
・ステップ切込み量:0.01mm/回
超音波スピンドル | 通常スピンドル |
---|---|
![]() 超音波スピンドルで加工した穴は鏡面になりました。 |
![]() 通常グラインディング加工ではクラックが深い為、鏡面にはなりませんでした。 |
石英ガラスにφ2.2ステップ穴加工を実施
・ダイヤモンド電着ツール#100を使用
・超音波あり/なしで穴壁面のダメージを観察
超音波スピンドル | 通常スピンドル |
---|---|
![]() ![]() 粒度が粗いダイヤモンド電着ツールでも超音波振動を加える事でダメージレス穴加工ができます! |
![]() ![]() |
目詰まり低減
・#400ダイヤモンド電着ツール穴加工
・目詰まりしやすい#400ダイヤモンド電着ツールで石英ガラスφ1.5穴加工実施。
・超音波なし→1穴目、目詰まりでツール破損
・超音波あり→5穴加工完了 まだまだ加工が可能です
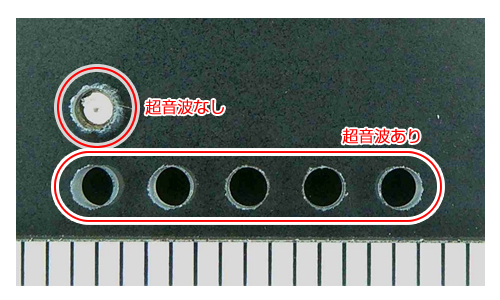
シリコンウエハ(Siウエハ)ザグリ加工時、目詰まりとチッピング比較
超音波あり/なしで、ダイヤモンド電着ツール先端とザグリ穴表面のチッピングを比較しました。
加工時間、使用したツールは同じでも圧倒的に超音波スピンドルで加工した方が高品質です。
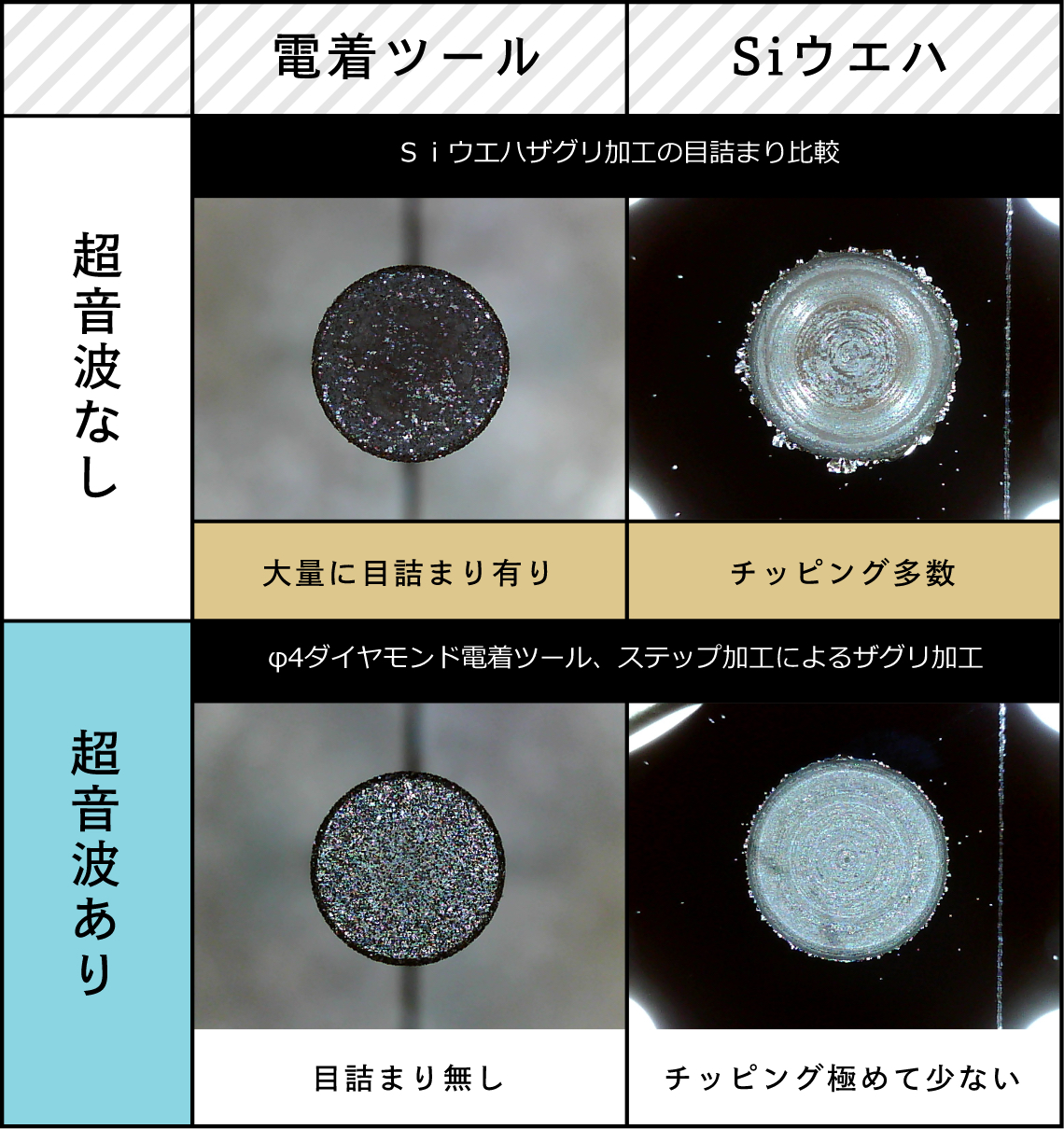
深穴加工 アスペクト比1:15
超音波スピンドルを使用するとアスペクト比1:15(直径:深さ)の深穴加工が誰でも簡単にできます。
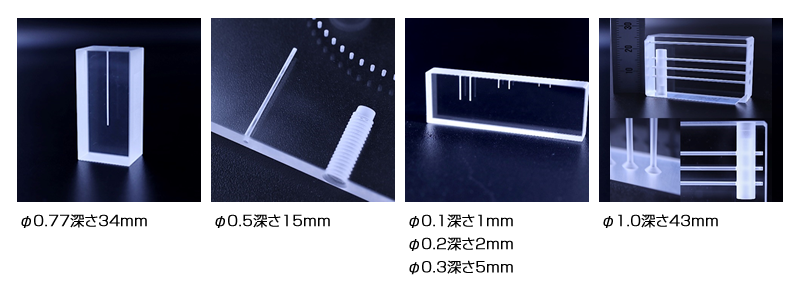
ツール寿命延長、加工穴径安定
超音波スピンドルでシリコンにφ0.42×深さ12.5mm穴加工実施。
#400ダイヤモンド電着ツール1本で232穴加工できました。
加工した穴径は全てφ0.42±0.013以内、穴径が安定しています。
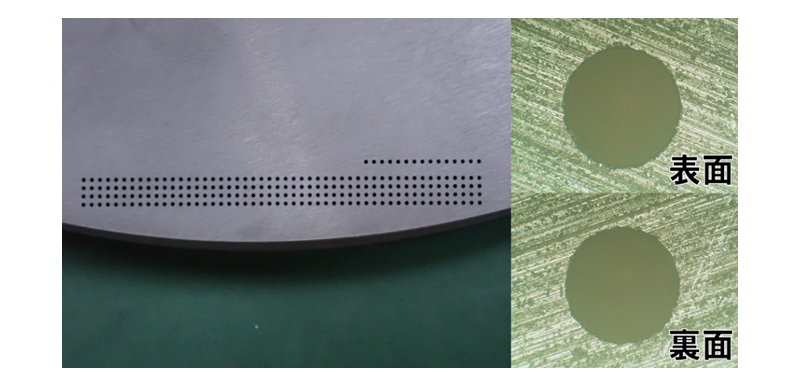
超音波加工ユニット製品紹介
超音波発振器 | |
---|---|
寸法 | 約150mm(幅)×262mm(高さ)×360mm(奥行) |
発振周波数 | 40kHz |
最大定格出力 | 200W |
重量 | 約6.8kg |
振幅可変 | フロントパネルのツマミあるいは制御ケーブルにて |
電源 | AC100V250VA |
モーターコントローラー | |
---|---|
寸法 | 約312mm(幅)×114mm(高さ)×254mm(奥行) |
定格電源電圧 | 1kVA |
重量 | 約1.5kg |
超音波スピンドル | |
---|---|
型式 | US-ssp-A4 |
寸法 | 外観図を参照ください。 |
重量 | 約5.8kg |
主軸回転数 | 最大15,000min-1 |
超音波周波数 | 40kHz |
冷却方式 | 水冷循環式 |
エアパージ | あり |
モーター | ブラシレスモーター最大定格500W |
-
◆積極的に「立会いテスト加工」を
行います株式会社 寿原テクノス福岡ファクトリーは立会いテスト加工を積極的に行っています。超音波スピンドルによる加工を実際にご覧いただき、通常のミーリング加工との違いを体感ください。
加工音、クーラントの量、チッピング量、送り速度など、目視で確認できない微細な超音波振動を触れて確認することができます。
-
-
◆最も重要なのは「アフターフォロー」
超音波スピンドルで脆性材料を加工する場合、加工パラメーターに「超音波出力(振幅量)」が加わるため、一般のミーリング加工と回転数、送り速度などが異なってきます。
初めて超音波スピンドルを導入されたお客様に対しては、お電話やメール等で丁寧かつ的確なアフターフォローを行い、万が一、お困りの際には全力で対応いたします。
・加工条件
・ダイヤモンド電着工具のメッシュサイズや形状
・クーラント
・クランプ方法 など
岳将製の超音波スピンドル・超音波アーバーのメンテンナスもお気軽にご相談ください。
-
導入の流れ
-
お問い合わせ
-
まずはお問い合わせフォーム、またはお電話にてご連絡ください。
-
案件の詳細確認と
目標設定 -
お客様がブレイクスルーしたい案件を詳細に打合せいたします。
加工には文章だけでは伝わらない細やかなニュアンスがあるため、現状の問題点、超音波加工機に求める性能や品質について、をできる限り、対面でお打合せを行いたいと考えています。
お客様と目線を合わせ、阿吽の呼吸になれる事が理想と考えています。
超音波加工の特徴をご理解いただき、機種の選定と加工目標を設定いたします。
-
テスト加工と立会い
-
超音波加工機で事前に条件出しなど、さまざまなテストを実施いたします。
テスト内容や結果、詳細の状況については、都度お客様へご連絡いたします。
目標を達成できる見込みが立ちましたら、テスト加工にお立会いいただく事を推奨しています。
実際の超音波加工をご覧いただき、最初から終わりまでの加工の工程をご確認ください。
-
受注と納品
-
ご注文書確認後、納期をご連絡いたします。
超音波加工機の使用方法などの詳細につきましては、超音波加工のエキスパートスタッフがお伺いし、十分に説明させていただきます。
必要な場合、その場で再現加工を実施いたします。
-
アフターフォロー
-
株式会社 寿原テクノス福岡ファクトリーは超音波加工機を購入いただいたお客様をずっとフォローし続けます。
新しい案件、異なった材質、加工条件の選定が上手く行かないなど、導入後のトラブル時もご安心ください。
今まで培ったノウハウでお客様をバックアップし続ける事を約束します。
安心してご購入ください。
よくある質問
-
-
市販のダイヤモンド電着ツール、ダイヤモンドコーティングドリル等が使用可能です。シャンク径はφ3、φ6が標準となっています。超音波振幅をz軸方向に発生させるため、ツールの長さ調整が必要となります。
-
-
超音波スピンドルは通常のミーリング加工に加えてz軸方向に超音波振幅が発生し、その振幅量を調整する事が可能です。弊社ではお客様の加工に最適な加工条件、ダイヤモンド電着砥石選定等、受託加工で培ったノウハウを提案させていただきます。
-
-
特にφ1以下の細穴加工、アスペクト比1:10以上の深穴加工、また細溝加工や深溝加工に効果を発揮します。超音波スピンドルは切りくず排出性が向上します。目詰まりしやすいSi(シリコン)等の材料にも非常に効果的でツール寿命が延長します。加工抵抗が小さくなりますのでガラス材料のチッピングを最小限に抑えることができます。
-
-
量産加工時の穴径の変化が小さい、加工速度向上、ツール寿命延長、クーラント少量で良いため機械へのダメージが少ないといったメリットがあります。
-
-
40kHz±1kHzとなります
-
-
Φ3とΦ6です
-
-
これまでの実績でΦ10です。
-
-
ベアリング、ブラシ、ローター、ブラシはご自身での交換が可能です。
-
-
約3~4ヵ月となっています。
-
-
主にガラス系、シリコンは超音波の効果がでやすくなっています。
-
-
超音波スピンドルは細深穴加工に効果がありますが、ミーリングには不向きです。
-
-
通常の水溶性クーラントを使用しています。
-
-
100Vです
-
-
現在はございません。日本国内のみになります。